Our Alcast Company Ideas
Our Alcast Company Ideas
Blog Article
A Biased View of Alcast Company
Table of ContentsAlcast Company - TruthsSome Known Incorrect Statements About Alcast Company Alcast Company for DummiesThe Only Guide to Alcast CompanyFacts About Alcast Company UncoveredThe Facts About Alcast Company Uncovered
The subtle difference depends on the chemical content. Chemical Comparison of Cast Aluminum Alloys Silicon promotes castability by minimizing the alloy's melting temperature and improving fluidness throughout casting. It plays a crucial role in permitting intricate mold and mildews to be filled up properly. Furthermore, silicon adds to the alloy's stamina and use resistance, making it useful in applications where sturdiness is critical, such as automotive parts and engine parts.It also boosts the machinability of the alloy, making it easier to process into finished items. In this means, iron contributes to the overall workability of aluminum alloys.
Manganese contributes to the toughness of light weight aluminum alloys and improves workability. Magnesium is a light-weight component that gives toughness and influence resistance to aluminum alloys.
Getting The Alcast Company To Work
It enables the manufacturing of lightweight components with excellent mechanical buildings. Zinc improves the castability of light weight aluminum alloys and aids control the solidification process during casting. It improves the alloy's strength and hardness. It is often found in applications where intricate forms and fine details are necessary, such as ornamental spreadings and particular auto components.
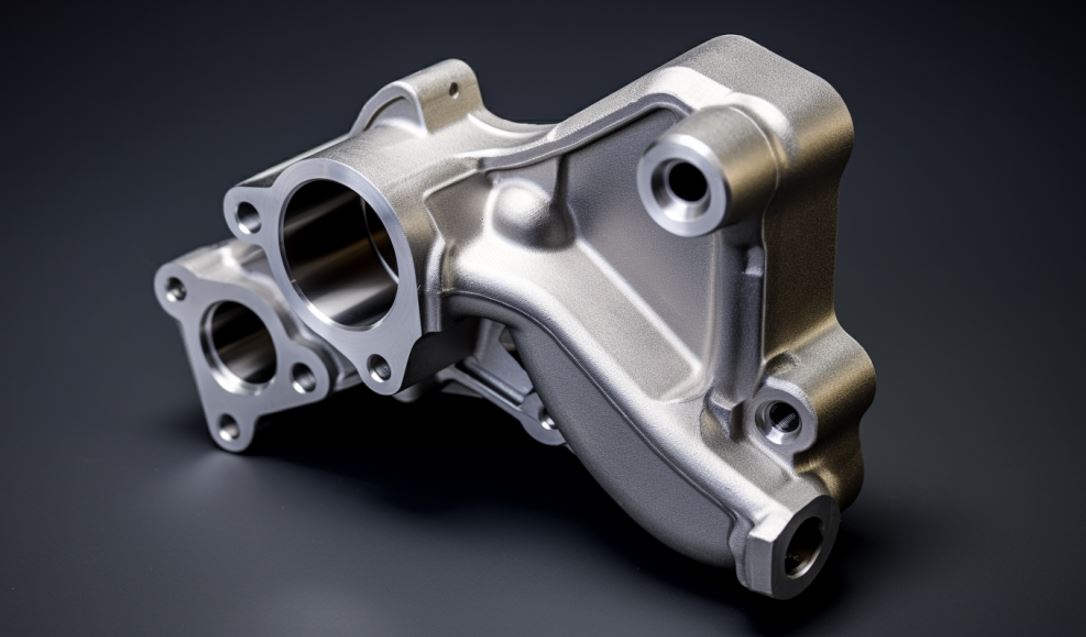
The main thermal conductivity, tensile toughness, yield toughness, and elongation vary. Select suitable raw materials according to the performance of the target item generated. Amongst the above alloys, A356 has the highest thermal conductivity, and A380 and ADC12 have the least expensive. The tensile limitation is the opposite. A360 has the most effective yield strength and the highest elongation price.
More About Alcast Company
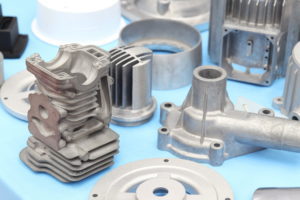
In precision spreading, 6063 is fit for applications where detailed geometries and premium surface finishes are vital. Examples consist of telecommunication rooms, where the alloy's superior formability permits for streamlined and aesthetically pleasing styles while preserving architectural integrity. In the Lights Solutions industry, precision-cast 6063 components create classy and efficient lighting components that require complex shapes and great thermal efficiency.
It leads to a finer surface finish and far better deterioration resistance in A360. In addition, the A360 exhibits premium elongation, making it optimal for complex and thin-walled elements. In precision spreading applications, A360 is fit for markets such as Consumer Electronics, Telecommunication, and Power Devices. Its enhanced fluidity enables detailed, high-precision elements like mobile phone casings and communication device housings.
See This Report on Alcast Company
Its one-of-a-kind buildings make A360 a valuable choice for accuracy spreading in these sectors, boosting product toughness and high quality. aluminum casting manufacturer. Aluminum alloy 380, or A380, is a commonly made use of casting alloy with a number of distinctive qualities.
In accuracy spreading, light weight aluminum 413 radiates in the Customer Electronics and Power Tools industries. This alloy's premium deterioration resistance makes it a superb selection for outside applications, guaranteeing lasting, resilient items in the stated markets.
Get This Report on Alcast Company
As soon as you have made a decision that the light weight aluminum pass away casting process appropriates for your task, a critical next action is picking one of the most ideal alloy. The aluminum alloy you pick will considerably affect both the spreading procedure and the properties of the end product. As a result of this, you should make your decision very carefully and take an informed approach.
Identifying one of the most ideal light weight aluminum alloy for your application will certainly mean evaluating a broad selection of attributes. These comparative alloy characteristics follow the North American Die Spreading Organization's guidelines, and we have actually separated them right into 2 classifications. The initial group addresses alloy attributes that affect the manufacturing process. The 2nd covers qualities impacting the residential or commercial properties of the last product.
The 10-Minute Rule for Alcast Company
The alloy you choose for die spreading straight affects numerous facets of the spreading procedure, like exactly how easy the alloy is to work with and if it is prone to casting issues. Hot fracturing, additionally called solidification splitting, is a normal die spreading defect for light weight aluminum alloys that can cause interior or surface-level tears or splits.
Specific light weight aluminum alloys are much more susceptible to hot cracking than others, and your choice needs to consider this. An additional usual problem located in the die spreading of light weight aluminum is pass away soldering, which is when the cast sticks to the die walls and makes ejection tough. It can harm both the actors and the die, so you ought to look for alloys with high anti-soldering residential properties.
Corrosion resistance, which is already a noteworthy quality of light weight aluminum, can differ considerably from alloy to alloy and is an essential particular to take into consideration depending upon the ecological conditions your product will be exposed to (aluminum casting manufacturer). Wear resistance is one more home commonly sought in light weight aluminum items and can differentiate some alloys
Report this page